- Home
- Sustainable development
- Environment
- Clean air at work
Clean air at work
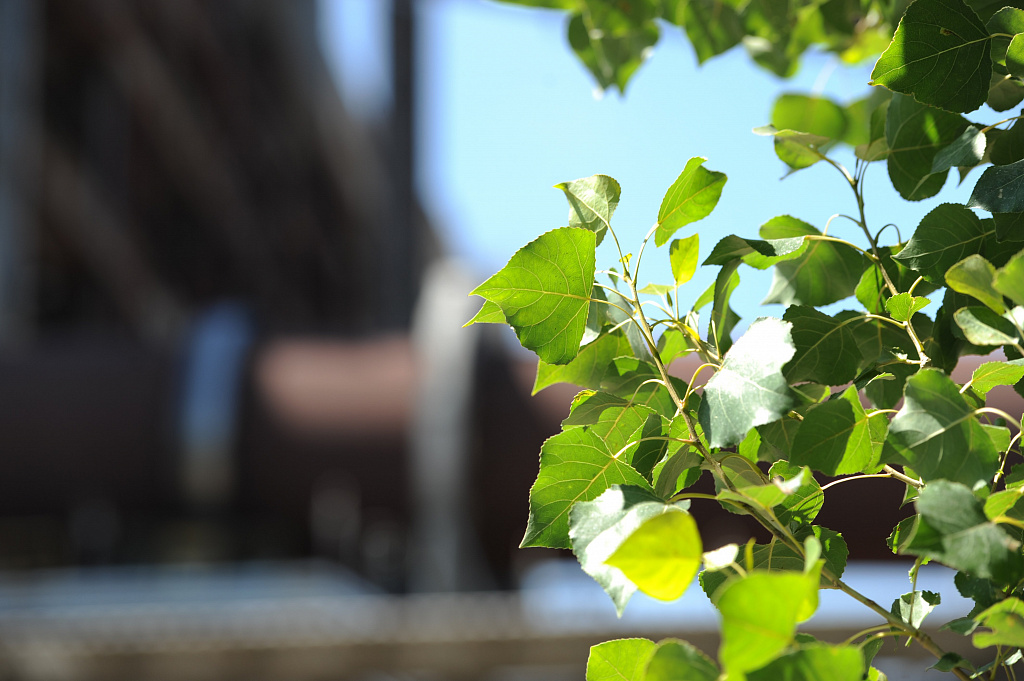
NLMK Group has been taking steps to reduce its impact on air quality for many years, improving working conditions and creating a clean environment in the surrounding areas. NLMK Group operates more than 500 advanced dust and gas cleaning facilities, which not only capture more than 98% of the substances, but also return them to production.
The results of this endeavour are already noticeable. Since 2000, NLMK Group's steel output has almost doubled, while its specific emissions have almost halved to 19.8 kg/t. Lipetsk, where NLMK Group's flagship production site is located, has become the cleanest steelmaking city in Russia.
These projects have already made an impact: despite almost doubling steel production since 2000, NLMK Group companies were able to nearly halve emissions to 20.3 kg per tonne of steel, which is very close to the best available technology level of 18.9 kg per tonne. Lipetsk, which is home to the Group’s main production site, has become the least polluted steelmaking city in Russia.
In 2019, NLMK Lipetsk equipped its coke and chemical operations with a chemical by-products recovery complex to ensure process stability, efficient coke-oven gas purification, and halve the shop’s air emissions. The Refractory Shop has completed the revamping of its dedusting unit. This will reduce local dust emissions by more than 90%, while the residual dust content of the purified air will meet the best world indicators at 5 mg/m3.
A new BF slag treatment facility was launched at NLMK Lipetsk in 2020. The project enables switching to anhydrous slag cooling technology, reducing the emission of hydrogen sulfide in the corresponding area by 3.5x and minimizing the smell from this chemical compound.